Hi all, I have aproject which requires my S7-200 to communicate with the PDMS through Modbus communcation. I must send some data to the PDMS, and recieve other control signals from the PDMS. As I understand from the S7-200 manual, the PLC can act as a master (sending Data), and a slave (Recieving data), Can the PLC work as both sending and recieving data at the same time, or its a totally different concept. I must send the PDMS the folloing points: Inputs f the PLC (total of 55 inputs). Outputs of the PLC (total of 40 outputs). Memory locations (regesters I use them in my control and I must inform the PDMS about them). I must recieve from the PDMS about 10 control points.
Read Digital Input Data From Modbus Slave S7 200 PLC.
Any one can help me with that, Does any one have sample programs using the modbus can share it. I found a tool here in the forums for testing the modbus communications, but its for **OPEN MODBUS / TCP Communication via CP343-1 and CP443-1**, is it adifferent protocol, can I use it with S7-200 CPU 224xp. If this tool cant be used with CPU 224xp, is there any tool to do that. To use the Modbus slave instructions in your S7-200 program, follow these steps: 1. Insert the MBUS_INIT instruction in your program and execute the MBUS_INIT instruction for one scan only. You can use the MBUS_INIT instruction either to initiate or to change the Modbus communications parameters. When you insert the MBUS_INIT instruction, several hidden subroutines and interrupt routines are automatically added to your program.
Use the Library Memory command to assign a starting address for the V memory required for Modbus Slave Protocol instructions. Place only one MBUS_SLAVE instruction in your program. This instruction is called every scan to service any requests that have been received. Connect the communications cable between Port 0 on the S7-200 and the Modbus master device.
CAUTIONInterconnecting equipment with different reference potentials can cause unwanted currents to flow through the interconnecting cable. These unwanted currents can cause communications errors or damage equipment.Ensure that all equipment that is connected with a communications cable either shares a common circuit reference or is isolated to prevent unwanted current flows. The accumulators (AC0, AC1, AC2, AC3) are utilized by the Modbus slave instructions and appear in the Cross Reference listing. Prior to execution, the values in the accumulators of a Modbus Slave instruction are saved and restored to the accumulators before the Modbus Slave instruction is complete, ensuring that all user data in the accumulators is preserved while executing a Modbus Slave instruction. The Modbus Slave Protocol instructions support the Modbus RTU protocol.
These instructions utilize the Freeport utilities of the S7-200 to support the most common Modbus functions. The following Modbus functions are supported: Function Description 1 Read single/multiple coil (discrete output) status. Function 1 returns the on/off status of any number of output points (Qs). 2 Read single/multiple contact (discrete input) status. Function 2 returns the on/off status of any number of input points (Is).
Flstudio 12 Regkey.reg Zip File Average ratng. If you found that any of above fl studio 12 reg key files may have been subject to copyright protection. FL Studio 12.2 + RegKey [c0bra].rar Archive rar +1. Downloading file in progress. FL Studio 12 0 2 with Key Reg.zip.zip. FL Studio 12.3 Crack Full Serial Number Download. FL studio 12.3 crack download zip. File Encryption XP 1.7.310 Crack Plus Serial Key. Fl studio 12 regkeyreg zip file free.
3 Read single/multiple holding registers. Function 3 returns the contents of V memory. Holding registers are word values under Modbus and allow you to read up to 120 words in one request.
4 Read single/multiple input registers. Function 4 returns Analog Input values.
5 Write single coil (discrete output). Function 5 sets a discrete output point to the specified value. The point is not forced and the program can overwrite the value written by the Modbus request. 6 Write single holding register.
Function 6 writes a single holding register value to the V memory of the S7-200. 15 Write multiple coils (discrete outputs). Function 15 writes the discrete output values to the Q image register of the S7-200.
The starting output point must begin on a byte boundary (for example, Q0.0 or Q2.0) and the number of outputs written must be a multiple of eight. This is a restriction for the Modbus Slave Protocol instructions. The points are not forced and the program can overwrite the values written by the Modbus request. 16 Write multiple holding registers. Function 16 writes multiple holding registers to the V memory of the S7-200. There can be up to 120 words written in one request.
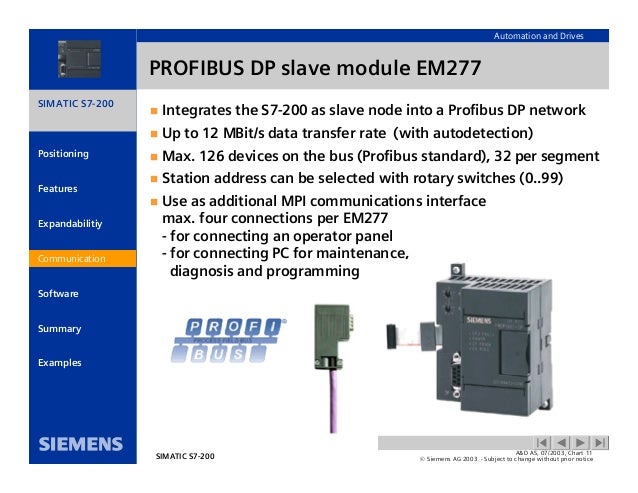
I was a little bit confused, does these functions used by the master device how it can be used. Please, Any one can help? Requests can only done by master device. Slaves wait for requests and don't do anything if there is no request from a master device. So if you configure you S7200 as master, you can use these functions to read/write on PDMS.
Also PDMS must be configured as slave device and must be write enabled for the signals you want to write to PDMS registers. Or PDMS can be master and do the same things to S7200 but this time S7200 must be slave and write enabled for signals you want to read from PDMS registers. I don't have examples for S7200 modbus configuration or program.